The Evolution from CAD to CNC: A Paradigm Shift in Manufacturing Efficiency
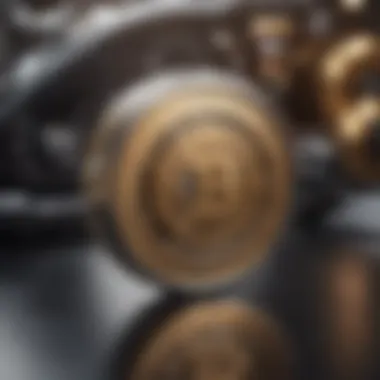
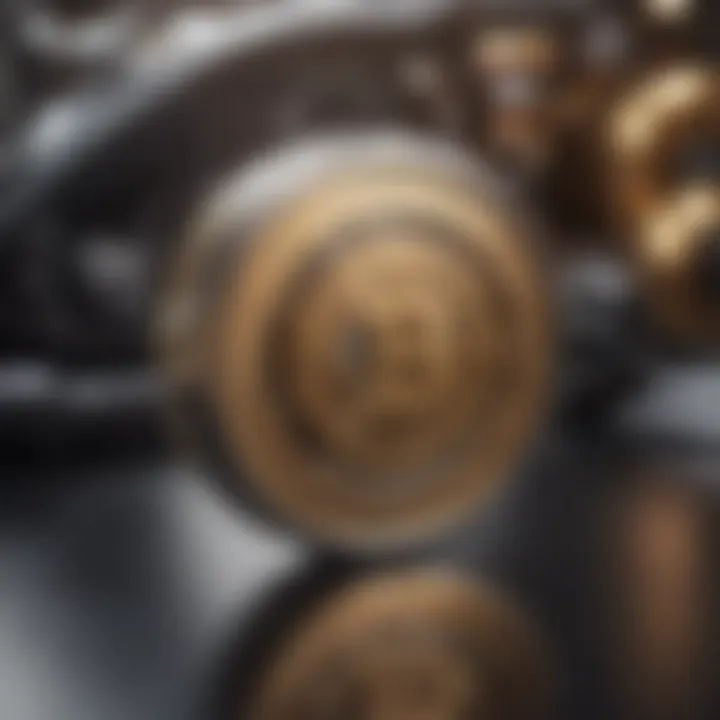
What is CAD to CNC:
CAD (Computer-Aided Design) to CNC (Computer Numerical Control) represents a transformative advancement in manufacturing technology. The genesis of CAD to CNC can be traced back to the pioneers in the field of computerized design and numerical control systems. This integration aims to streamline the manufacturing process, enhancing precision, efficiency, and automation capabilities. Various iterations and adaptations of CAD to CNC have emerged over time, each refining and optimizing the functionality to meet unique industrial requirements.
Who created the CAD to CNC? The initial concept of CAD to CNC was developed by visionaries in the engineering and manufacturing sectors seeking innovative solutions to traditional production challenges. Collaborations between software developers, engineers, and industry experts led to the evolution of CAD to CNC technology as we know it today.
How many CAD to CNC systems are there? The market boasts several CAD to CNC systems, each offering distinct features and functionalities tailored to specific manufacturing needs. Companies continuously refine and expand their CAD to CNC offerings to provide comprehensive solutions for a diverse range of industries.
Does the CAD to CNC serve a purpose? Indeed, CAD to CNC serves a crucial purpose in modern manufacturing by elevating precision, enhancing efficiency, and enabling automation in production processes. The integration of CAD to CNC facilitates the creation of complex geometries with utmost accuracy, driving quality and productivity in manufacturing operations.
What is the CAD to CNC used for? CAD to CNC technology finds applications in various industries, including aerospace, automotive, electronics, and healthcare. From prototyping to mass production, CAD to CNC enables manufacturers to optimize design processes, streamline production workflows, and deliver high-quality products cost-effectively.
The CAD to CNC tokenomics depend on several key tokens that govern the functioning of the system, ensuring secure transactions, data integrity, and seamless operability within the manufacturing ecosystem.
The CAD to CNC ecosystem encompasses a myriad of tools and software, ranging from CAD software for design modeling to CNC controllers for precise machining operations. This comprehensive suite of tools integrates seamlessly to enable end-to-end manufacturing solutions, from concept to production.
But why would one opt to swap CAD to CNC instead of trading? The primary distinction lies in the context of manufacturing operations. Swapping CAD to CNC entails transitioning from the design phase to the production phase, where the digital model is translated into physical components with the precision and efficiency afforded by CNC technology.
How can one buy CAD to CNC? Acquiring CAD to CNC typically involves procuring software licenses, CNC machines, and related equipment from reputable suppliers and vendors. Manufacturers must assess their specific needs and production requirements to determine the most suitable CAD to CNC solutions for their operations.
Introduction
The realm of manufacturing has witnessed a paradigm shift with the evolution from CAD to CNC technologies, a transition that has revolutionized traditional processes to an extent never seen before. This article delves deep into the intricacies of this evolution, exploring how precision, efficiency, and automation have been significantly impacted by the integration of CAD and CNC technologies. The seamless coordination between Computer-Aided Design (CAD) and Computer Numerical Control (CNC) has paved the way for enhanced productivity and unparalleled accuracy within the manufacturing sector.
Understanding CAD and CNC
The concept of CAD
In the realm of design and engineering, Computer-Aided Design (CAD) has established a crucial position by offering a digitized platform for creating detailed models of products and components. The backbone of modern design processes, CAD software enables engineers to visualize and simulate products in a virtual environment before physical prototypes are even created. The key characteristic of CAD lies in its ability to facilitate precise geometric representation and dimensional accuracy, ensuring that designs are translated flawlessly into the manufacturing phase. While CAD systems vary in complexity and features, their universal appeal stems from the efficiency and flexibility they provide in translating concepts into tangible designs.
The principle of CNC
On the other hand, Computer Numerical Control (CNC) embodies the automation aspect of modern manufacturing, where machining tools and equipment are controlled via programmed commands and parameters. The fundamental principle of CNC lies in its ability to execute intricate machining tasks with utmost precision and repeatability, eliminating the margin for human error in manufacturing processes. Through the utilization of CNC machines, manufacturers can achieve high levels of productivity and consistency in part production. The unique feature of CNC lies in its adaptability to diverse manufacturing requirements, allowing for the fabrication of complex components with unparalleled accuracy and efficiency.
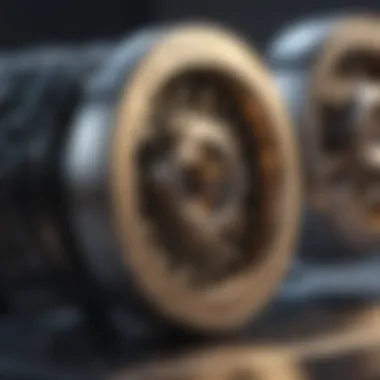
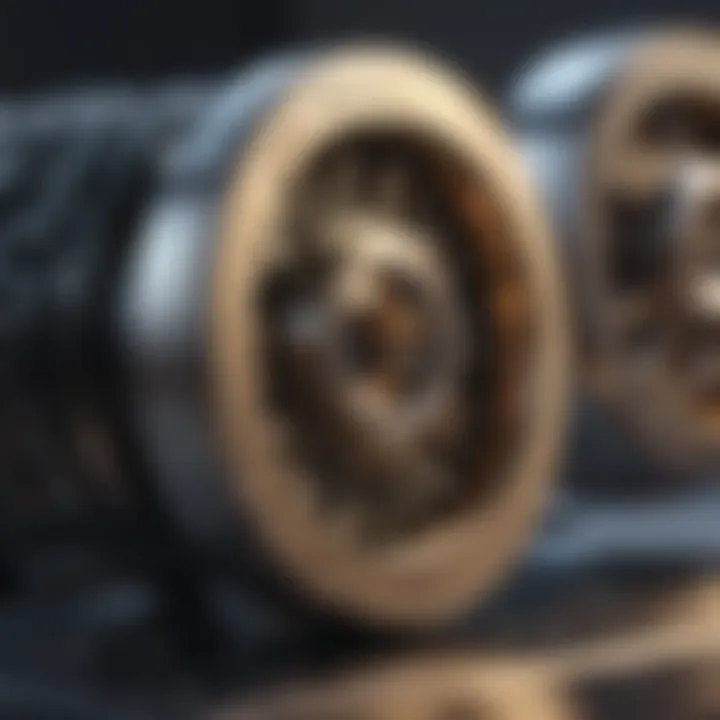
Importance of CAD-CNC Integration
Enhanced design capabilities
The integration of CAD and CNC technologies has empowered designers with enhanced capabilities to visualize and optimize product designs with advanced simulations and prototyping. By leveraging CAD tools alongside CNC machining processes, manufacturers can refine designs iteratively, ensuring that the final product meets exact specifications and performance requirements. The seamless synchronization between CAD and CNC promotes a holistic approach to design and production, enabling manufacturers to push the boundaries of innovation while maintaining stringent quality standards.
Streamlined manufacturing processes
One of the most significant advantages of integrating CAD and CNC is the optimization of manufacturing workflows resulting in streamlined processes. By directly translating CAD designs into CNC programming instructions, manufacturers can reduce production lead times, minimize material wastage, and enhance overall operational efficiency. The dynamic synergy between CAD design and CNC machining ensures that design changes can be implemented swiftly, leading to agile manufacturing processes that adapt to market demands efficiently.
CAD Technology Advancements
In this section of the article, we delve into the essential advancements within CAD technology that have reshaped manufacturing processes. CAD (Computer-Aided Design) has significantly revolutionized the way designs are created and translated into physical products. The integration of CAD with manufacturing processes has led to enhanced precision, efficiency, and automation in the industry. By focusing on CAD Technology Advancements, we explore the specific elements that have contributed to the evolution towards more streamlined and effective manufacturing methods.
3D Modeling and Simulation
Virtual Prototyping
Virtual prototyping is a pivotal aspect of CAD technology advancements that have had a profound impact on the manufacturing sector. This technique allows for the creation of virtual models of products, facilitating accurate visualization and testing before actual production. The key characteristic of virtual prototyping lies in its ability to detect design flaws and improve product functionalities early in the design process. Virtual prototyping serves as a beneficial choice for this article as it promotes error reduction, cost savings, and faster time-to-market for manufactured goods. Its unique feature lies in the ability to simulate real-world conditions, enabling manufacturers to make informed decisions based on virtual testing. However, challenges such as software complexities and the initial investment in simulation tools may pose potential disadvantages.
Simulation of Manufacturing Processes
Simulation of manufacturing processes is another crucial element in CAD technology advancements. This area focuses on simulating various production scenarios to optimize efficiency and quality. The key characteristic of simulation lies in its capacity to identify bottlenecks, improve workflow, and minimize risks in manufacturing operations. It is a popular choice for this article as it allows manufacturers to analyze different production strategies without physical prototyping. The unique feature of simulation is its ability to predict performance outcomes and troubleshoot potential issues before production commences. While simulation offers significant advantages in terms of time and cost savings, potential disadvantages may include a learning curve for complex simulation software and the need for skilled personnel to interpret simulation results effectively.
Parametric Design Features
Parametric design features play a vital role in enhancing CAD technology advancements and shaping modern manufacturing processes. These features offer designers flexibility and automation in making design modifications, contributing to increased productivity and precision. The flexibility in design modifications aspect allows for quick and efficient changes to designs through parameter adjustments. This characteristic is beneficial for this article as it enables manufacturers to adapt to evolving project requirements efficiently. The unique feature of flexibility in design modifications is its ability to create parametric relationships between design elements, ensuring design coherence and consistency throughout the project. However, challenges such as the complexity of parametric design tools and the potential for errors in setting parameters may be considered as disadvantages.
Automated Design Changes
Automated design changes represent a significant advancement in CAD technology that streamlines the design modification process. This feature automates repetitive design tasks and updates interconnected design elements automatically. The key characteristic of automated design changes is its capacity to reduce manual intervention in design revisions, leading to faster design iterations and enhanced efficiency. It is a popular choice for this article as it accelerates design cycles and minimizes the potential for human errors during modifications. The unique feature of automated design changes lies in its ability to maintain design consistency across multiple iterations, ensuring that all design elements remain coherent. While automated design changes offer substantial advantages in terms of time savings and error reduction, challenges such as the need for continuous parameter maintenance and potential system complexities may be considered as drawbacks.
CNC Machining Advancements

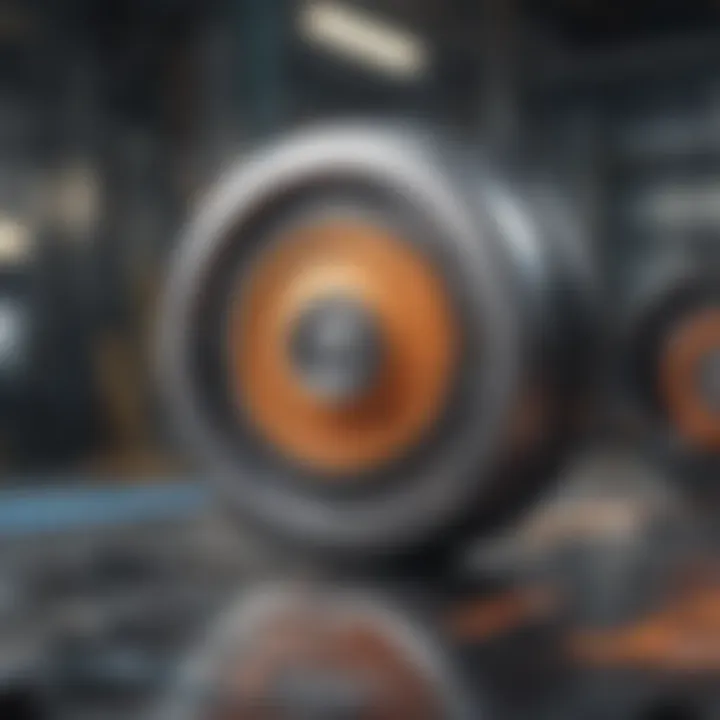
High-Speed Machining
- Improved Efficiency
Improved Efficiency
The aspect of improved efficiency within CNC machining advancements is fundamental in enhancing overall production efficacy. By enabling high-speed operations and streamlined processes, improved efficiency ensures optimized resource utilization and time management. The key characteristic of improved efficiency lies in its ability to achieve higher output levels within shorter time frames, boosting productivity while maintaining precision standards. This feature presents a valuable choice for manufacturers seeking to expedite production timelines without compromising quality. An essential benefit of improved efficiency is the reduction of idle time during machining operations, leading to enhanced overall manufacturing performance.
- Reduction in Production Time
Reduction in Production Time
The reduction in production time is a critical aspect contributing to the efficiency enhancements brought about by CNC machining advancements. By minimizing the time taken to complete production cycles, manufacturers can meet demand requirements more effectively and respond swiftly to market dynamics. The key characteristic of this reduction lies in its ability to optimize the manufacturing process by streamlining workflows and minimizing delays. For this article, the unique feature of reduced production time significantly improves operational flexibility and responsiveness to changing production needs. It's advantageous in scenarios where rapid turnaround times are essential, providing a competitive edge in time-sensitive industries.
Multi-Axis Machining
- Complex Geometries Fabrication
Complex Geometries Fabrication
The capability of multi-axis machining to handle complex geometries fabrication is a standout feature making it an integral element of CNC machining advancements. This aspect contributes significantly to the manufacturing of intricate components that require precise detailing and sophisticated designs. The key characteristic of complex geometries fabrication is its ability to execute intricate machining operations from multiple angles, resulting in the creation of components with high intricacy and accuracy. This capability makes it a preferred choice for industries like aerospace and automotive, where complex part geometries are commonplace. However, a disadvantage could be the increased complexity in programming and setup to achieve the desired outcomes.
- Enhanced Cutting Precision
Enhanced Cutting Precision
Enhanced cutting precision stands out as a key attribute in multi-axis machining, elevating the overall quality standards of manufactured parts. The ability to achieve superior cutting accuracy across various axes enhances the surface finish, dimensional accuracy, and overall quality of machined components. The key characteristic of enhanced cutting precision lies in its capacity to execute intricate cuts with unmatched accuracy, ensuring the fulfillment of stringent tolerance requirements. For this article, the unique feature of enhanced cutting precision offers manufacturers a competitive edge by delivering components with exceptional precision and quality. However, one potential disadvantage could be the higher level of skill and expertise required to operate and maintain machines with enhanced cutting precision.
CAD-CNC Integration Benefits
In understanding the comprehensive evolution from CAD to CNC technologies, the integration of both systems offers a myriad of benefits that profoundly impact manufacturing processes. The seamless combination of CAD and CNC results in enhanced precision βοΈ, efficiency π οΈ, and productivity π€. By bridging the gap between design and production through CAD-CNC integration, manufacturers can achieve unparalleled levels of accuracy and automation.
Enhanced Precision and Accuracy
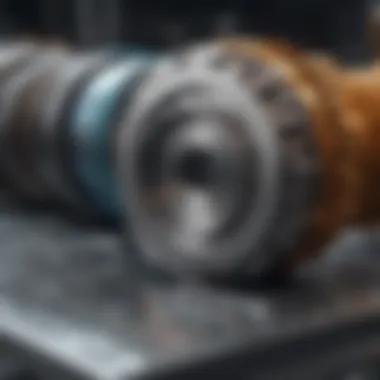
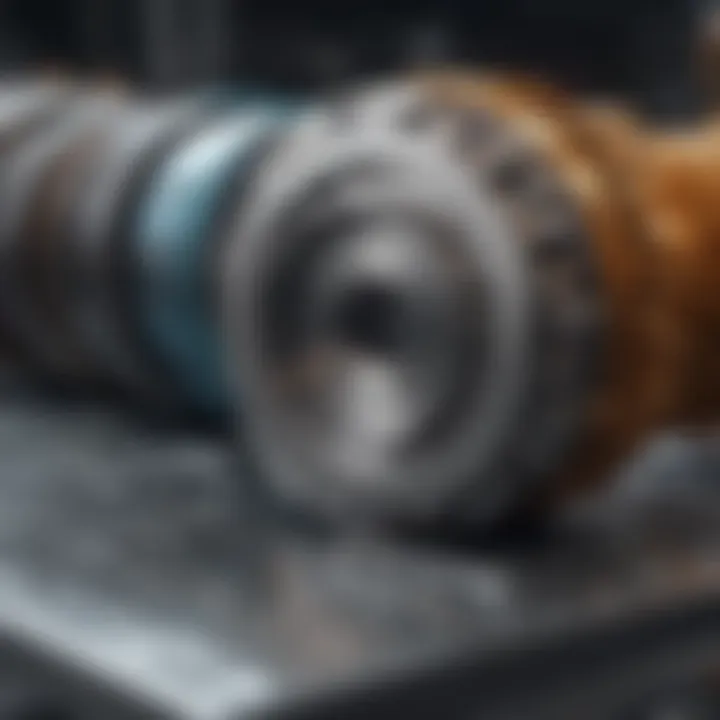
Tight Tolerances Achieved
The achievement of tight tolerances plays a pivotal role in ensuring the precision and quality of manufactured components. When CAD designs are seamlessly translated into CNC instructions, the resulting output exhibits meticulous attention to detail and minimal deviation from the intended specifications. Tight tolerances allow for the creation of complex geometries with utmost accuracy, perfect for applications necessitating intricate parts or components. Manufacturers rely on tight tolerances to meet stringent quality standards and exceed customer expectations, positioning it as an indispensable aspect of the CAD-CNC integration benefits.
Elimination of Human Errors
By mitigating the risks associated with human intervention, the elimination of human errors stands out as a prominent advantage of CAD-CNC integration. Traditional manufacturing processes are inherently susceptible to human inaccuracies, ranging from manual measurement errors to unintentional design discrepancies. With CAD-CNC integration, these pitfalls are significantly reduced as automated systems ensure consistent execution of tasks with minimal to no room for human-induced mistakes. This eradication of human errors not only enhances the overall quality of the produced components but also amplifies operational efficiency by streamlining workflows and reducing rework instances, making it a critical aspect of the benefits offered by CAD-CNC integration.
Increased Production Efficiency
Optimized Manufacturing Processes
Optimizing manufacturing processes through CAD-CNC integration revolutionizes the production landscape by providing manufacturers with the capacity to streamline operations and enhance workflow efficiency. By harnessing the power of CAD design and CNC machining, manufacturers can reduce lead times, optimize resource utilization, and expedite the overall production cycle. Integrating CAD models directly into CNC systems eliminates redundancy and accelerates the transition from design to manufacturing, resulting in a seamless and uninterrupted workflow. This optimization not only boosts productivity but also improves resource allocation, making optimized manufacturing processes a cornerstone of the efficiency gains derived from CAD-CNC integration.
Reduced Material Wastage
A key highlight of CAD-CNC integration benefits is the substantial reduction in material wastage achieved through precise control and optimization of cutting processes. CNC machines, fueled by CAD designs, facilitate precise material removal, ensuring maximal utilization of raw materials and minimizing scrap generation. By programming CNC machines to execute intricate cuts with minimal margins for error, manufacturers can significantly cut down on material wastage, thereby reducing production costs and environmental impact. This reduction in material wastage not only contributes to cost savings but also aligns with sustainable manufacturing practices, positioning it as a critical advantage of CAD-CNC integration benefits.
Future Trends in CAD-CNC Technology
The evolution from CAD to CNC has paved the way for looking ahead at the future trends in CAD-CNC technology, ushering in a new era of innovation and advancement in manufacturing processes. As industries evolve and technology continues to progress at a rapid pace, staying abreast of upcoming trends is crucial for businesses aiming to maintain a competitive edge in the market. Future trends in CAD-CNC technology encompass a multitude of aspects that promise to revolutionize manufacturing even further, optimizing processes, enhancing productivity, and ensuring higher precision levels.
AI and Machine Learning Integration
Predictive maintenance
Predictive maintenance stands out as a pivotal element in the integration of AI and machine learning within CAD-CNC technologies. This approach involves leveraging data and analytics to predict when equipment maintenance will be required, thereby preemptively addressing issues before they escalate. In the context of CAD-CNC technology, predictive maintenance plays a significant role in ensuring uninterrupted manufacturing operations by minimizing downtime and optimizing machine performance. The key characteristic of predictive maintenance lies in its proactive nature, enabling manufacturers to identify potential faults or breakdowns before they occur.
Process optimization
Process optimization through AI and machine learning integration represents another noteworthy aspect of future trends in CAD-CNC technology. By employing algorithms and data analysis, manufacturers can streamline their processes, enhance operational efficiencies, and fine-tune the entire production cycle. This optimized approach not only boosts productivity but also contributes to cost savings and resource utilization. The unique feature of process optimization lies in its ability to dynamically adjust and improve manufacturing operations based on real-time data insights, leading to continuous enhancements in workflow and output quality.
Additive Manufacturing Innovations
3D printing advancements
Within the realm of additive manufacturing innovations, 3D printing advancements have emerged as a revolutionary force, reshaping how components and products are fabricated. The key characteristic of 3D printing lies in its ability to construct intricate geometries and complex structures with unprecedented precision and customization options. This innovation presents a viable choice for manufacturers seeking cost-effective, rapid prototyping solutions without compromising on quality. The unique feature of 3D printing advancements is its versatility in material usage, allowing for the creation of designs that were previously challenging to produce using traditional methods.
Material customization
Material customization represents a pivotal aspect of additive manufacturing innovations, offering manufacturers the flexibility to tailor material properties according to specific requirements. By customizing materials at a microscopic level, companies can achieve superior product performance, functionality, and durability. The key characteristic of material customization is its ability to create bespoke components that align precisely with desired specifications, delivering heightened efficiency and performance outcomes. While material customization presents significant advantages in terms of product optimization, challenges such as material compatibility and processing complexity need to be carefully navigated to maximize its benefits within the CAD-CNC integration landscape.