Mastering the Art of Expanding Machines: A Comprehensive Guide
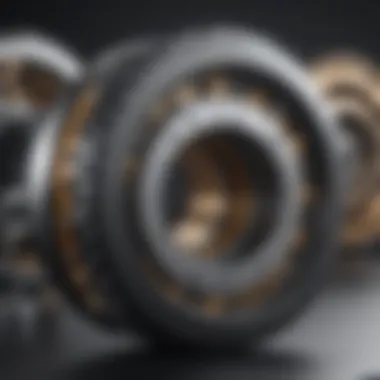
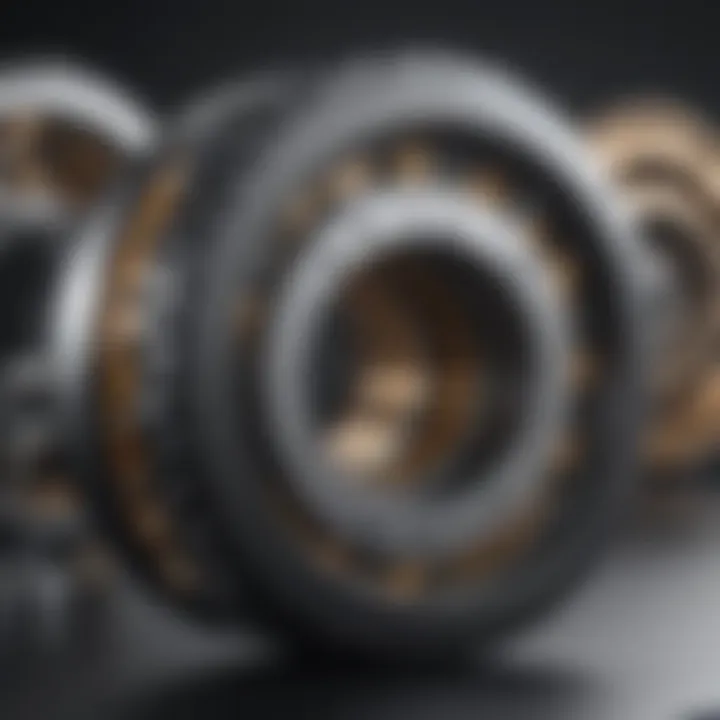
What is an Expanding Machine:
An expanding machine is a sophisticated piece of equipment designed to enhance the scalability of various operations within industrial settings. This revolutionary invention has a fascinating history behind its creation, with credit attributed to pioneering engineers who sought to streamline and automate manufacturing processes. Different types of expanding machines exist, tailored to specific industries and manufacturing requirements, showcasing the versatility and adaptability of this technology.
The primary purpose of an expanding machine is to facilitate the expansion of materials such as metal, plastics, or textiles with precision and efficiency. By employing intricate mechanisms and advanced technology, expanding machines can stretch, shape, or manipulate materials according to predefined specifications, ensuring consistent results and high-quality output. The industry landscape has significantly benefited from the adoption of expanding machines, driving innovation and efficiency across a wide range of applications.
In the realm of crypto and blockchain, the concept of expending machines has gained traction, offering a unique approach to streamline transactions and enhance liquidity. Tokenomics plays a crucial role in determining the value and utility of expending machines, with various tokens contributing to the ecosystem's functionality and stability. Alongside tokenomics, a diverse set of tools form an integral part of the expending machine ecosystem, providing users with the necessary infrastructure and resources to engage effectively with this innovative concept.
When considering the decision to swap expending machines instead of trading them, nuanced differences come into play. The distinction lies in the underlying mechanisms and processes involved in swapping assets compared to traditional trading activities. Understanding these differences is essential for individuals looking to engage with expending machines effectively and efficiently.
Purchasing an expanding machine involves navigating through established platforms and exchanges that support the exchange of tokens. The process typically entails creating an account, conducting thorough research on the available options, and executing transactions based on individual preferences and requirements. By following these steps and leveraging the available resources, enthusiasts can access expanding machines and explore the potential benefits they offer within the crypto landscape.
Introduction to Expanding Machines
Expanding machines play a crucial role in various industries, revolutionizing production processes and fostering efficiency. As we delve into the realm of expanding machines in this article, we uncover the intricate mechanisms and applications that make them indispensable tools for modern manufacturing.
Understanding Expanding Machines
Definition of Expanding Machines
Expanding machines refer to specialized equipment designed to widen or stretch materials efficiently. Their primary function lies in enhancing the dimensions and properties of different materials, including fabrics, papers, and metals. The versatility of expanding machines allows for the customization of expansion techniques to suit specific production needs. This key characteristic of adaptability ensures that expanding machines are a preferred choice for industries seeking precision and quality enhancement. Despite their advantages in streamlining processes, expanding machines also present challenges like maintenance complexities and initial investment costs.
Historical Evolution
The evolution of expanding machines traces back to the industrial revolution when manual stretching and spreading methods were prevalent. Over time, technological advancements led to the mechanization of these processes, giving rise to more sophisticated expanding machines. The historical progression highlights the continuous quest for efficiency and precision in material processing. This narrative of development underscores the importance of innovation in shaping the expanding machine landscape, marking a shift towards automation and smart manufacturing solutions.
Significance in Modern Industries
In modern industries, expanding machines have become indispensable assets across various sectors, including textiles, paper manufacturing, and metalworking. Their significance lies in streamlining production processes, ensuring product quality, and driving operational efficiency. By utilizing expanding machines, businesses can achieve consistency in product dimensions, enhance surface finishes, and optimize material usage. The integration of expanding machines in modern industries signifies a strategic investment in technological innovation to stay competitive in evolving markets.
Basic Components
Rollers and Belts

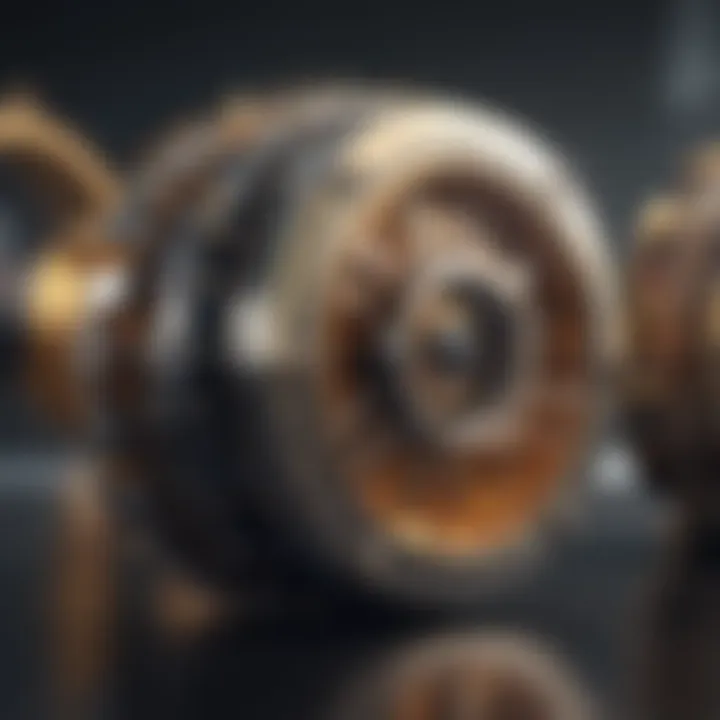
Rollers and belts are fundamental components of expanding machines, facilitating the movement and manipulation of materials during the expansion process. The key characteristic of rollers and belts is their ability to ensure uniform stretching and spreading of materials, contributing to precise outcomes. Their design promotes efficient material handling and aids in achieving desired expansion results. While rollers and belts enhance machine functionality, factors like wear and tear issues pose challenges that require regular maintenance and monitoring for optimal performance.
Control Systems
Control systems in expanding machines govern the automation and regulation of expansion processes, enabling operators to monitor and adjust various parameters. The key characteristic of control systems is their role in managing speed, tension, and alignment during material expansion, ensuring consistent results. The incorporation of advanced control systems enhances the efficiency and accuracy of expanding machines, offering operational flexibility and adaptability to changing production demands. However, the complexity of control systems necessitates skilled personnel for maintenance and troubleshooting to minimize downtime and maximize productivity.
Measurement Instruments
Measurement instruments are essential components of expanding machines that provide critical data on material dimensions and expansion outputs. The key characteristic of measurement instruments is their ability to accurately gauge and record expansion parameters, facilitating quality control and process optimization. By utilizing precise measurement instruments, operators can maintain product consistency, meet quality standards, and identify potential improvements in the expansion process. The integration of measurement instruments enhances the overall effectiveness of expanding machines but requires calibration and regular upkeep to ensure measurement accuracy for reliable outcomes.
Mechanisms and Operation
In the realm of expanding machines, understanding the mechanisms and operation is paramount. This section delves deep into the core functioning of these machines, shedding light on their intricate design and operational significance within various industries. By dissecting the components and processes involved in these machines, we gain a profound insight into their essential role in production and manufacturing processes. Exploring the mechanisms and operations provides a comprehensive understanding of how expanding machines contribute to efficiency, productivity, and product quality.
Principles of Operation
Expansion Techniques
Expansion techniques are a vital aspect of the operational framework of expanding machines. They encompass a range of methods aimed at altering the dimensions and properties of materials with precision and efficiency. These techniques play a significant role in achieving desired outcomes in manufacturing processes by providing versatility and scalability. The key characteristic of expansion techniques lies in their ability to tailor the material properties according to specific requirements, making them a popular choice for a diverse range of applications. Despite their advantages, expansion techniques may encounter limitations in terms of speed or material compatibility, which need to be carefully considered for optimal use in various industries.
Control Mechanisms
Control mechanisms govern the operational parameters of expanding machines, ensuring precision, consistency, and safety during the manufacturing process. The crux of control mechanisms lies in their ability to regulate critical aspects such as speed, pressure, and material flow to achieve desired outcomes. Their key characteristic is the fine-tuning capability that allows operators to adjust settings for different materials and production requirements, making them a beneficial choice for maintaining quality standards. However, complexities in control mechanisms may pose challenges in terms of setup and maintenance, requiring expertise and advanced training for optimal implementation.
Material Handling
Material handling plays a vital role in streamlining the flow of materials within expanding machines, optimizing efficiency, and minimizing waste. The key characteristic of material handling is its ability to ensure smooth transitions between various stages of the manufacturing process, enhancing overall productivity and reducing downtime. Its unique feature lies in the integration of automated systems for material transport, storage, and retrieval, improving operational efficiency and reducing manual intervention. Despite these advantages, material handling systems may face challenges related to maintenance costs and integration with existing production setups, necessitating careful consideration for seamless implementation.
Applications in Various Industries
Exploring the crucial role of expanding machines in various industries is paramount to understanding their versatile applications. Industries such as the textile sector, paper manufacturing, and metalworking benefit greatly from the utilization of expanding machines. These machines play a vital role in enhancing efficiency, improving quality, and streamlining production processes in a myriad of applications. Understanding the specific requirements of each industry enables the tailored use of expanding machines to optimize results and meet industry standards effectively.
Textile Industry
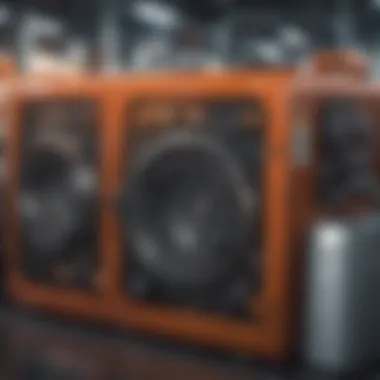
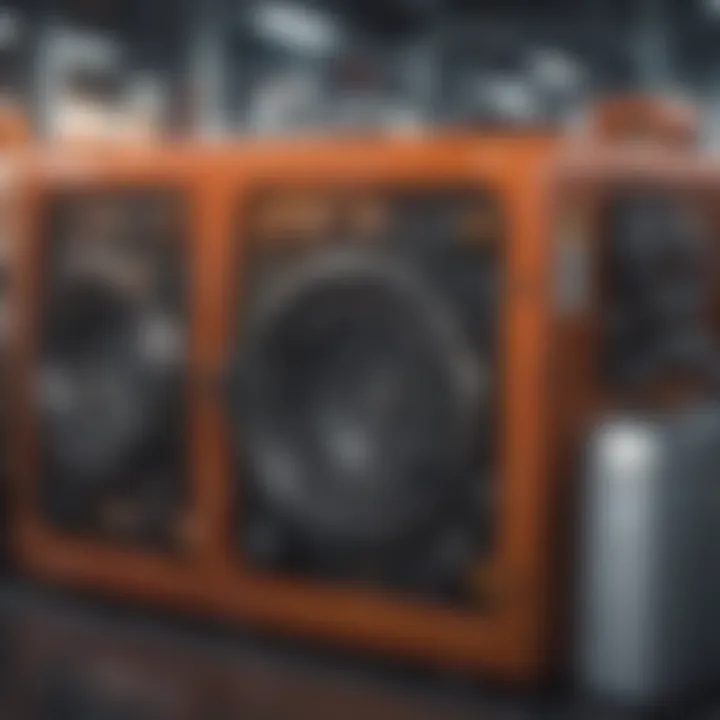
Fabric Processing
Fabric processing stands as a cornerstone in the textile industry, pivotal in transforming raw materials into high-quality fabrics. The intricate process involves weaving, dyeing, printing, and finishing fabrics to create unique textures and designs. Expanding machines play a crucial role in fabric processing by ensuring precise stretching and spreading of fabrics, contributing to improved tensile strength and uniformity. The ability of expanding machines to handle various fabric types, from delicate silks to durable denims, showcases their versatility and efficiency in fabric processing. While enhancing the overall quality and appearance of fabrics, expanding machines streamline production processes, reducing lead times and improving overall production output.
Garment Production
Garment production represents the culmination of fabric processing, where fabrics are tailored and assembled into finished garments. The integration of expanding machines in garment production expedites cutting, sewing, and assembly processes, resulting in higher production efficiency and accuracy. By utilizing expanding machines for fabric spreading and relaxation, the garment industry ensures consistent fabric handling, minimizing material wastage and enhancing final garment quality. The precision and speed of expanding machines in garment production lead to increased productivity, reduced labor costs, and improved competitiveness in the dynamic fashion market.
Quality Control
Quality control holds a paramount position in the textile industry, ensuring that fabrics and garments meet stringent quality standards and regulatory requirements. Expanding machines facilitate quality control measures by providing accurate tension control, width adjustment, and defect detection capabilities during fabric processing and garment production. The integration of intelligent sensors and monitoring systems in expanding machines enables real-time quality assessment, enhancing production efficiency and minimizing defects. By incorporating quality control mechanisms in expanding machines, textile manufacturers can uphold product consistency, meet customer expectations, and elevate their brand reputation in the competitive textile market.
Paper Manufacturing
Production Processes
The production processes in paper manufacturing encompass pulp preparation, paper formation, pressing, drying, and finishing stages, requiring precision and efficiency for optimal paper quality. Expanding machines play a vital role in the paper industry by ensuring uniform web tension, accurate trimming, and controlled web spreading during the production process. By integrating expanding machines in production processes, paper manufacturers can enhance paper formation, improve caliper consistency, and optimize overall product quality. The flexibility and adaptability of expanding machines in handling various paper grades and sizes enhance production versatility, enabling paper manufacturers to meet diverse market demands efficiently.
Quality Enhancement
Quality enhancement forms a critical aspect of paper manufacturing, focusing on improving paper properties such as smoothness, strength, brightness, and printability. Expanding machines contribute to quality enhancement by enabling precise coating application, controlled moisture content, and accurate web guiding in paper production. The incorporation of expanding machines in quality enhancement processes ensures uniform fiber distribution, reduced web breaks, and enhanced surface finish of paper products. By utilizing expanding machines for quality enhancement, paper manufacturers can achieve superior paper quality, increased production yields, and enhanced customer satisfaction in the competitive paper market.
Efficiency Improvement
Efficiency improvement serves as a core objective in paper manufacturing, aiming to optimize production processes, reduce waste, and enhance productivity. Expanding machines play a pivotal role in efficiency improvement by maximizing machine speed, minimizing downtime, and improving web handling efficiency in paper mills. The automated control systems and advanced technologies integrated into expanding machines streamline production workflows, reduce setup times, and enhance overall operational efficiency. By incorporating efficiency improvement strategies through expanding machines, paper manufacturers can achieve cost savings, energy efficiency, and sustainable practices in paper production, ensuring long-term competitiveness in the ever-evolving paper industry.
Metalworking Sector
Sheet Metal Processing
Sheet metal processing constitutes a fundamental part of the metalworking sector, encompassing cutting, bending, and shaping metal sheets for various industrial applications. Expanding machines play a crucial role in sheet metal processing by providing precise metal stretching, leveling, and trimming capabilities. The accuracy and repeatability of expanding machines in sheet metal processing ensure high-quality metal parts, reduced material waste, and enhanced production efficiency. By leveraging expanding machines for sheet metal processing, metalworking industries achieve cost-effective metal forming processes, seamless production integration, and improved material utilization, catering to diverse market demands effectively.
Forming Operations
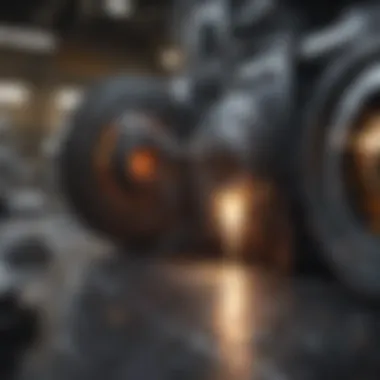
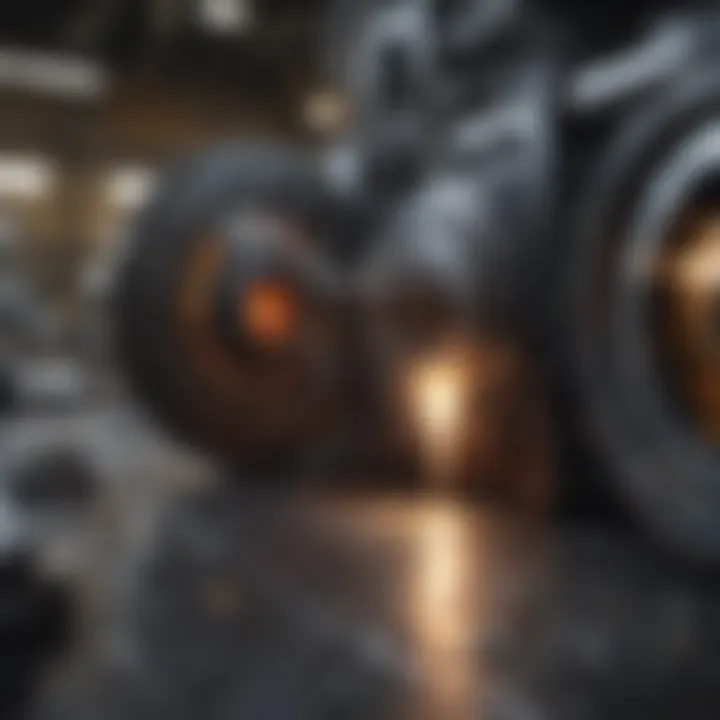
Forming operations in metalworking involve the shaping and molding of metal components through processes like stamping, forging, and extrusion. Expanding machines contribute significantly to forming operations by offering controlled material expansion, surface finishing, and dimensional accuracy in metal part production. The versatility and precision of expanding machines enable intricate forming operations, complex part geometries, and rapid prototyping in metalworking applications. By employing expanding machines for forming operations, metalworking industries optimize production cycles, reduce tooling costs, and enhance part quality, ensuring efficient metal component manufacturing and competitive market positioning.
Surface Finishing
Surface finishing plays a crucial role in metalworking, enhancing the aesthetic appeal, corrosion resistance, and functionality of metal products. Expanding machines play a pivotal role in surface finishing by providing uniform brushing, polishing, and deburring capabilities on metal surfaces. The precision and consistency offered by expanding machines in surface finishing ensure superior surface quality, improved paint adhesion, and enhanced product durability. By integrating expanding machines into surface finishing processes, metalworking industries achieve high-quality surface treatments, efficient production output, and customer satisfaction in delivering aesthetically pleasing and durable metal products to diverse industries.
Advanced Techniques and Innovations
The section on Advanced Techniques and Innovations plays a pivotal role in enhancing the discourse of this comprehensive guide on expanding machines. By delving into cutting-edge methodologies and innovations, this segment sheds light on the future horizons of expanding machines within various industries. The exploration of advanced techniques aims to provide readers with a nuanced understanding of the evolving landscape of machine expansion.
Automation and Robotics
Industry Integration
Industry 4.0 Integration stands at the forefront of technological advancements in expanding machines. This integration leverages digitalization and automation to streamline manufacturing processes, enhance efficiency, and improve overall productivity. The key characteristic of Industry 4.0 Integration lies in its ability to connect machines, products, and humans through the Internet of Things (IoT) and data exchange. This seamless interconnectivity facilitates real-time monitoring, predictive maintenance, and data-driven decision-making. The unique feature of Industry 4.0 Integration is its emphasis on cyber-physical systems, enabling intelligent and autonomous manufacturing environments. While its advantages include increased operational transparency and flexibility, potential disadvantages may arise from cybersecurity risks and initial investment costs.
Precision Engineering
Precision Engineering embodies the pursuit of perfection in machine design and operation. This discipline focuses on achieving the highest levels of accuracy, reliability, and repeatability in manufacturing processes. The key characteristic of Precision Engineering lies in its meticulous attention to detail and high-quality standards. Its meticulous approach ensures precise control over dimensional tolerances, material properties, and operational parameters. Precision Engineering is a popular choice for this article as it underscores the importance of precision in expanding machines, where nanometer-level accuracy can make a significant difference in product quality and performance. Advantages of Precision Engineering include refined product quality, reduced waste, and enhanced customer satisfaction. However, challenges such as cost-intensive tools and expertise requirements might be considered as disadvantages.
AI Applications
AI Applications inject intelligence and adaptive capabilities into expanding machines, revolutionizing how tasks are performed and optimized. The key characteristic of AI Applications is their ability to analyze vast amounts of data, learn from patterns, and make data-driven decisions autonomously. AI enables expanding machines to adapt to changing production needs, optimize energy consumption, and predict maintenance requirements. This innovative technology is a beneficial choice for this article as it showcases the transformative power of artificial intelligence in enhancing operational efficiency and performance. The unique feature of AI Applications lies in their capacity to continuously improve algorithms and decision-making processes through machine learning. Advantages of AI Applications encompass enhanced productivity, reduced downtime, and predictive maintenance capabilities. Nevertheless, concerns about data privacy, algorithm bias, and integration complexities may pose as potential disadvantages to consider.
Smart Manufacturing
Io
T in Expanding Machines
IoT in Expanding Machines integrates interconnected sensors and devices to enable data exchange and remote monitoring capabilities. This technology plays a crucial role in collecting real-time data on machine performance, operational efficiency, and product quality. The key characteristic of IoT in Expanding Machines is its ability to create a digital thread between machines, enabling seamless communication and data sharing across the manufacturing ecosystem. IoT integration is a beneficial choice for this article as it highlights the importance of connectivity and data-driven insights in enhancing expanding machine operations. The unique feature of IoT in Expanding Machines is its capacity to enable predictive maintenance, optimize production schedules, and enhance supply chain visibility. Advantages include improved decision-making, resource optimization, and operational efficiency, while potential disadvantages may include data security vulnerabilities and interoperability challenges.
Data Analytics
Data Analytics empowers manufacturers to derive actionable insights from vast data sets generated by expanding machines. This analytical approach involves collecting, organizing, and analyzing data to identify patterns, trends, and performance metrics. The key characteristic of Data Analytics lies in its ability to transform raw data into meaningful information for strategic decision-making and process optimization. Data Analytics is a popular choice for this article as it underscores the importance of leveraging data to drive continuous improvement and operational excellence in expanding machines. The unique feature of Data Analytics is its predictive modeling capabilities, which enable manufacturers to forecast outcomes, optimize processes, and mitigate risks. Advantages of Data Analytics encompass increased efficiency, cost savings, and enhanced quality control. However, challenges related to data quality, interpretation complexity, and upskilling requirements may be considered as potential disadvantages.
Supply Chain Optimization
Supply Chain Optimization focuses on enhancing the efficiency and effectiveness of supply chain operations within expanding machine industries. This optimization strategy aims to streamline production processes, reduce lead times, and minimize inventory costs. The key characteristic of Supply Chain Optimization is its holistic approach to aligning supply chain activities with business goals and customer demands. Supply Chain Optimization is a beneficial choice for this article as it emphasizes the critical role of supply chain management in maximizing operational performance and competitiveness. The unique feature of Supply Chain Optimization is its ability to leverage data-driven insights, automation, and collaboration to optimize logistics, procurement, and distribution processes. Advantages include improved inventory management, cost reductions, and improved customer service levels. Potential disadvantages may include supply chain disruption risks, implementation complexities, and resistance to change.