Unlocking the Transformative Power of MDT CAD in Modern Engineering Practices
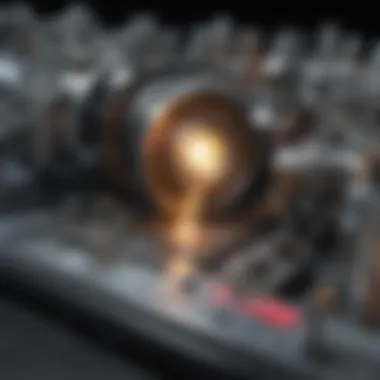
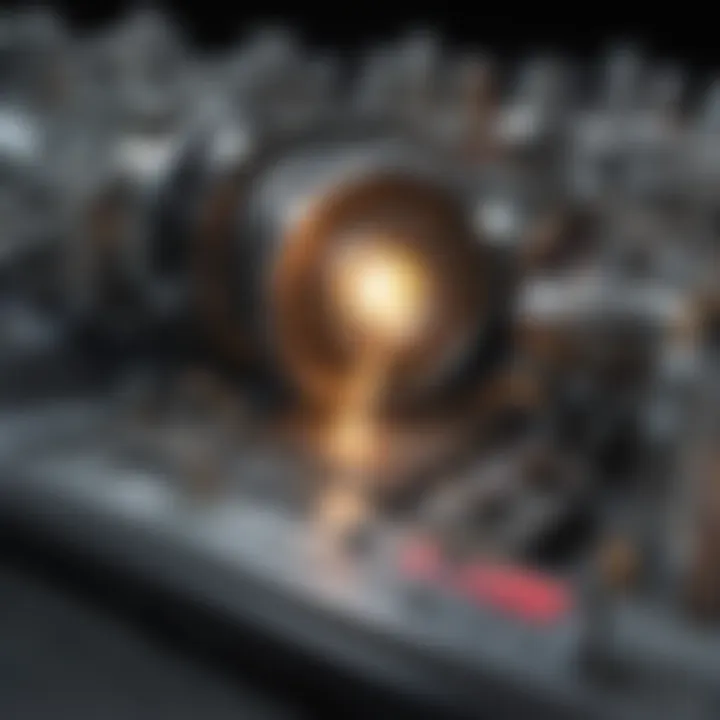
What is MDT CAD:
MDT CAD stands for Mechanical Design and Tooling Computer-Aided Design, a cutting-edge technology that has significantly impacted modern engineering practices. Originating from the innovative minds of software developers specializing in engineering applications, MDT CAD has revolutionized the way designers and manufacturers approach their craft. Unlike traditional CAD systems, MDT CAD focuses specifically on mechanical design and tooling, providing tailored solutions for enhanced precision and efficiency.
Being a specialized branch of CAD, MDT CAD offers a variety of tools and functionalities to support engineers in creating intricate designs and optimizing manufacturing processes. From 3D modeling to simulation and analysis, MDT CAD serves a crucial role in streamlining workflows and ensuring the seamless transition from concept to production.
MDT CAD is utilized across various industries, including automotive, aerospace, and machinery, where intricate mechanical components require precise design and manufacturing. Its primary purpose is to expedite the product development cycle, reduce errors in design, and improve overall productivity. This technology is indispensable for engineers seeking to meet strict quality standards and tight deadlines.
The framework of MDT CAD revolves around a set of tokens that govern its ecosystem. These tokens play a vital role in facilitating transactions within the platform, incentivizing users, and maintaining the stability of the MDT CAD network. Additionally, the ecosystem comprises essential tools such as rendering engines, finite element analysis software, and collaborative platforms, all integrated to enhance the user experience and streamline design processes.
When considering transactions within the MDT CAD ecosystem, the terms "swap" and "trade" often arise. While both actions involve the exchange of tokens, there is a subtle yet significant difference between them. Swapping MDT CAD tokens typically refers to converting one type of cryptocurrency for another, often on decentralized exchanges, whereas trading involves buying or selling tokens on various platforms, including centralized exchanges. Understanding this contrast is crucial for users engaging in transactions within the MDT CAD ecosystem, as it influences the method and implications of their crypto interactions.
To acquire MDT CAD tokens, users can navigate through several avenues, predominantly through cryptocurrency exchanges and decentralized platforms. By following a simple process of account creation, verification, and funding, individuals can purchase MDT CAD tokens and start engaging with the platform's features and functionalities. It is recommended for users to exercise caution and adhere to security measures when acquiring tokens to ensure a safe and efficient transaction process.
Introduction to MDT CAD
Mechanical Design and Tooling Computer-Aided Design (MDT CAD) plays a pivotal role in revolutionizing modern engineering practices, offering a comprehensive set of tools and functionalities that enhance design precision, manufacturing efficiency, and overall productivity within the engineering realm. By integrating advanced technologies and innovative design approaches, MDT CAD facilitates seamless collaboration and streamlines the design process, ultimately leading to unprecedented levels of efficiency and accuracy.
Defining MDT CAD
History of CAD Technology
The History of CAD Technology represents a significant milestone in the evolution of engineering design, marking the transition from manual drafting to computer-aided design processes. This key aspect of MDT CAD encapsulates the historical development of CAD software, showcasing the progression towards sophisticated modeling techniques and advanced tooling capabilities. The historical context provided by the History of CAD Technology contributes immensely to our understanding of the foundations upon which modern design practices are built, highlighting the continuous innovation and advancement in CAD technologies.
Overview of MDT CAD Applications
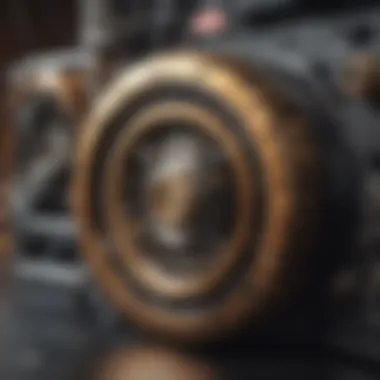
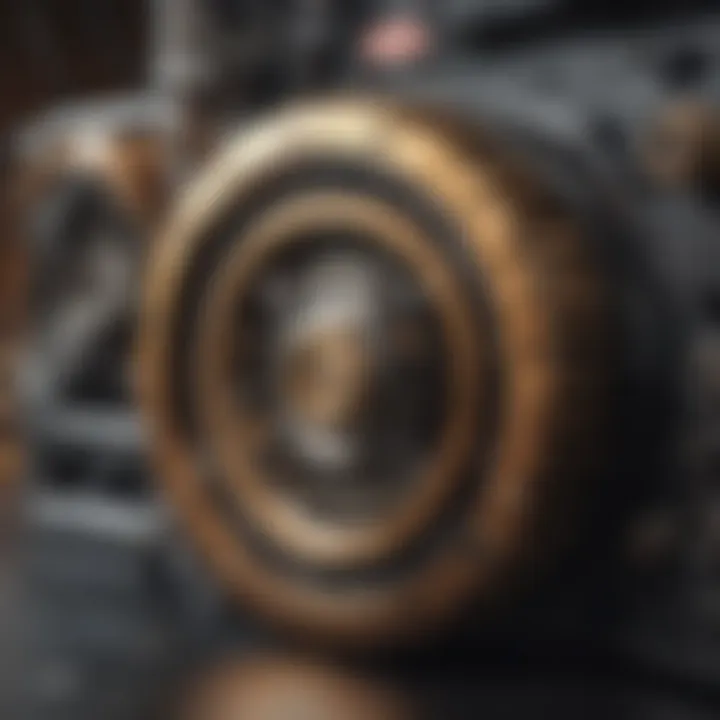
The Overview of MDT CAD Applications delves into the diverse range of functionalities and applications that MDT CAD offers to engineering professionals. From designing intricate components to simulating complex mechanisms, MDT CAD applications cover a broad spectrum of engineering requirements, catering to various industries and projects. This aspect of MDT CAD underscores its versatility and adaptability in addressing the evolving needs of the engineering landscape, making it a crucial tool for engineering design and development.
Evolution of CAD Software
Shift to 3D Modeling
The evolution of CAD software towards 3D modeling signifies a paradigm shift in design visualization and representation. The transition from traditional 2D drafting to 3D modeling opens up new possibilities for exploring complex geometries, improving spatial awareness, and optimizing design aesthetics. By embracing 3D modeling capabilities, engineers can create more realistic and detailed designs, leading to enhanced prototyping and visualization of final products.
Integration of Simulation Tools
The integration of simulation tools empowers engineers to conduct virtual analyses and tests within the CAD environment, enabling them to optimize designs and evaluate performance criteria with precision. By uniting design and simulation processes seamlessly, CAD software facilitates iterative design refinement and reduces the need for physical prototypes, consequently saving time and resources. This integration enhances the overall design quality and ensures that products meet rigorous performance standards.
Significance of MDT CAD in Engineering
Precision Engineering
Precision Engineering emphasizes the critical role of accuracy and meticulousness in engineering design, underscoring the importance of precise geometrical configurations and dimensional tolerances. MDT CAD enables engineers to achieve unparalleled levels of precision in design, ensuring that every component and assembly aligns with the specified requirements and functional parameters. This focus on precision engineering guarantees product quality and reliability, leading to enhanced performance and customer satisfaction.
Design Optimization
Design Optimization involves the iterative process of refining designs to enhance efficiency, functionality, and cost-effectiveness. MDT CAD provides engineers with sophisticated optimization tools that analyze design parameters, identify potential improvements, and streamline the design iterations for optimal results. By leveraging advanced algorithms and computational methods, design optimization within MDT CAD maximizes the performance potential of engineering solutions while minimizing material waste and production overheads.
Enhanced Engineering Design Processes
Enhanced Engineering Design Processes play a pivotal role in shaping modern engineering practices. With the advent of MDT CAD, the importance of streamlining and optimizing design processes has become even more crucial. By leveraging MDT CAD tools effectively, engineers can achieve unparalleled levels of precision, efficiency, and innovation in their design workflows. This section explores the specific elements, benefits, and considerations associated with Enhanced Engineering Design Processes within the context of MDT CAD.
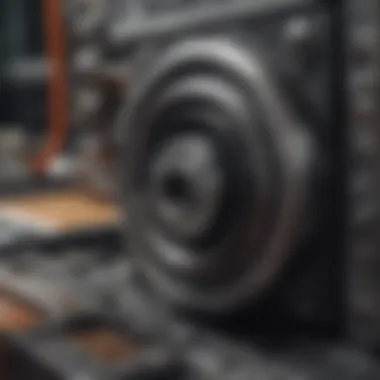
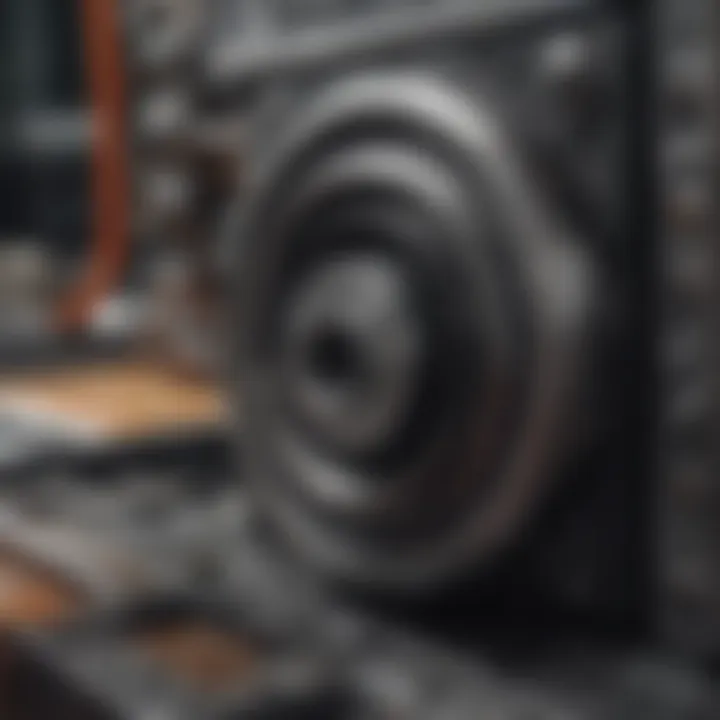
MDT CAD Tools Impact
Virtual Prototyping
Virtual Prototyping stands out as a cornerstone of MDT CAD tools, offering engineers the ability to create virtual models of their designs and test them in realistic simulations before physical production. Its key characteristic lies in enabling engineers to visualize and optimize their designs in a digital environment, thereby reducing the need for costly physical prototypes. Virtual Prototyping is a popular choice in this article due to its ability to save time, costs, and resources associated with traditional prototyping methods. One unique feature of Virtual Prototyping is its capacity to identify design flaws and inefficiencies early in the development process, ultimately leading to enhanced design outcomes. While Virtual Prototyping offers numerous advantages, such as flexibility and accuracy, potential disadvantages include the need for specialized training and software investment.
Parametric Modeling
Parametric Modeling is another indispensable aspect of MDT CAD tools, providing engineers with the ability to create intelligent, adaptable 3D models that can be easily modified and updated based on predefined parameters. Its key characteristic lies in enabling engineers to establish relationships between different components of a design, facilitating quick iterations and design changes. Parametric Modeling is a beneficial choice for this article due to its emphasis on design flexibility and automation, which aligns with the efficiency goals of modern engineering practices. One unique feature of Parametric Modeling is its ability to create complex designs with ease while maintaining consistency across iterations. The advantages of Parametric Modeling include design automation and error reduction, although challenges such as complex model dependencies may pose drawbacks in certain scenarios.
Streamlining Manufacturing
Streamlining Manufacturing is a critical aspect impacted by MDT CAD tools, as it focuses on optimizing production processes and improving overall manufacturing efficiency. This section delves into the specific aspects of CAM Integration and Additive Manufacturing Advancements within the context of MDT CAD and their contributions to enhancing manufacturing operations.
CAM Integration
CAM Integration plays a vital role in bridging the gap between design and manufacturing processes by enabling seamless communication and data transfer from CAD software to manufacturing machinery. Its key characteristic lies in automating the production process, reducing manual intervention, and maximizing production output. CAM Integration is a popular choice for this article due to its ability to streamline manufacturing workflows, minimize errors, and improve production consistency. One unique feature of CAM Integration is its ability to generate precise toolpaths and optimize machining strategies for diverse manufacturing requirements. While CAM Integration offers significant advantages in terms of efficiency and quality control, potential disadvantages may include high initial setup costs and the need for skilled personnel.
Additive Manufacturing Advancements
Additive Manufacturing Advancements represent a transformative shift in manufacturing methodologies, where layers of material are gradually added to create complex 3D objects. Its key characteristic lies in the freedom it provides designers to create intricate geometries that were previously impossible with traditional manufacturing techniques. Additive Manufacturing Advancements are a beneficial choice for this article due to their potential to revolutionize prototyping, customization, and on-demand production processes in the engineering sector. One unique feature of Additive Manufacturing Advancements is their ability to reduce material waste and introduce new design possibilities through layer-by-layer construction. The advantages of Additive Manufacturing Advancements include rapid prototyping and design complexity, yet challenges such as limited material selection and slow production speeds may impact certain applications.
Collaborative Design Advantages
Collaborative Design Advantages encompass the benefits of teamwork and real-time interaction within the design process, facilitated by MDT CAD tools. This section explores the specific aspects of Global Team Coordination and Real-Time Feedback, highlighting their importance in promoting collaboration, creativity, and efficiency in engineering design scenarios.
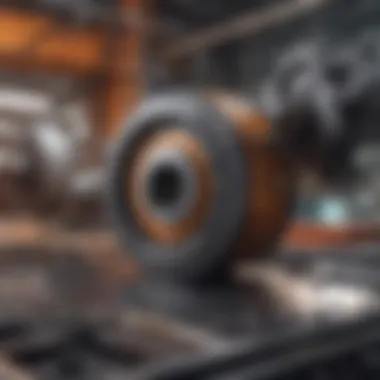
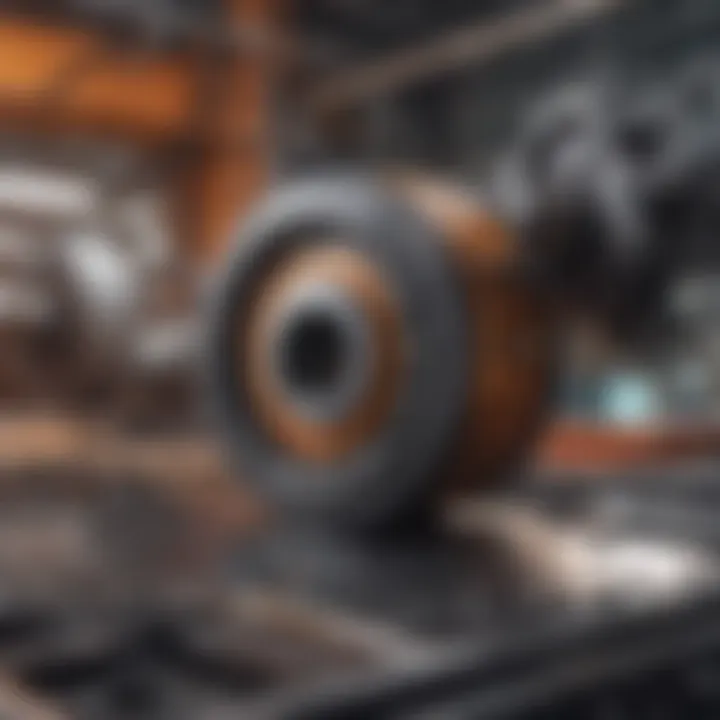
Global Team Coordination
Global Team Coordination underscores the significance of remote collaboration and coordination among geographically dispersed team members in engineering projects. Its key characteristic lies in fostering communication, sharing of ideas, and leveraging diverse expertise from different parts of the world. Global Team Coordination is a valuable choice for this article due to its role in breaking down geographical barriers, enabling round-the-clock work cycles, and consolidating global talent pools for collaborative design projects. One unique feature of Global Team Coordination is its ability to integrate cultural perspectives and technical insights, enriching the design process with varied viewpoints. While the advantages of Global Team Coordination include diverse skill sets and expanded project horizons, challenges such as communication barriers and time zone differences may require efficient management strategies.
Real-Time Feedback
Real-Time Feedback serves as a crucial mechanism for instant communication and iterative design improvements during the engineering design phase. Its key characteristic lies in providing immediate insights, corrections, and approvals on design iterations, facilitating quick decision-making and agile design processes. Real-Time Feedback is a popular choice for this article due to its ability to enhance design responsiveness, reduce design cycle times, and enable real-time collaboration among team members. One unique feature of Real-Time Feedback is its capacity to capture design changes in real-time, allowing teams to address issues promptly and adapt designs based on immediate feedback. The advantages of Real-Time Feedback include enhanced collaboration and error identification, although challenges such as data privacy concerns and information overload may affect its implementation in certain contexts.
Future Prospects of MDT CAD
In this section focusing on the future prospects of MDT CAD within the context of modern engineering practices, it is paramount to delve into the dynamic landscape that lies ahead in the realm of Computer-Aided Design. The incorporation of cutting-edge technologies and innovative solutions continues to shape the trajectory of MDT CAD, offering a glimpse into the potential advancements that will revolutionize the engineering industry.
Innovations in CAD Industry
Artificial Intelligence Integration
Artificial Intelligence Integration stands at the forefront of driving efficiency and accuracy in MDT CAD systems. Through the infusion of AI algorithms and machine learning capabilities, CAD programs can now automate complex design tasks, streamline workflows, and enhance predictive modeling. The key characteristic of Artificial Intelligence Integration lies in its ability to analyze vast datasets and iteratively improve design outcomes, resulting in optimized engineering processes. This advanced functionality offers substantial benefits in terms of reducing human error, accelerating design iterations, and unlocking new levels of design optimization. However, it is important to acknowledge the potential drawbacks related to data privacy and the need for comprehensive training to fully leverage the potential of AI integration within MDT CAD systems.
Cloud-Based CAD Solutions
Cloud-Based CAD Solutions represent a significant shift towards scalable and collaborative design platforms that transcend geographical barriers. The key characteristic of Cloud-Based CAD lies in its ability to centralize design data, facilitate real-time collaboration among diverse teams, and provide flexibility in accessing design tools from remote locations. This approach offers benefits such as enhanced version control, increased data security, and improved scalability for engineering projects. The unique feature of Cloud-Based CAD Solutions is the seamless integration of design data across multiple devices and locations, ensuring continuity in workflows and enhancing efficiency. While Cloud-Based CAD Solutions offer undeniable advantages in terms of accessibility and collaboration, considerations regarding data security, network stability, and upfront investment must be carefully evaluated.
Challenges and Opportunities
Cybersecurity Concerns
Cybersecurity Concerns pose a critical consideration in the adoption and advancement of MDT CAD technologies. The key characteristic of cybersecurity concerns in CAD systems pertains to safeguarding proprietary design data, preventing unauthorized access, and mitigating potential cyber threats that could compromise sensitive information. Addressing cybersecurity risks is imperative to maintain the integrity of engineering designs and protect intellectual property. The unique feature of cybersecurity measures lies in the implementation of encryption protocols, access controls, and regular security audits to fortify CAD systems against cyberattacks. While cybersecurity measures are essential for data protection, challenges may arise in balancing robust security measures with user accessibility and operational efficiency.
Sustainability Initiatives
Sustainability Initiatives in MDT CAD underscore the industry's shift towards environmentally conscious design practices and resource-efficient manufacturing processes. The key characteristic of sustainability initiatives within CAD is the integration of eco-friendly materials, energy-efficient design methodologies, and life cycle assessments to minimize the environmental impact of engineering projects. This approach not only reduces carbon footprints but also promotes sustainable development across various engineering sectors. The unique feature of sustainability initiatives lies in fostering a holistic approach to design that considers environmental, social, and economic factors to drive innovation and long-term viability. While sustainability initiatives offer substantial advantages in promoting eco-conscious design practices and enhancing corporate social responsibility, challenges may arise in balancing sustainability goals with traditional metrics of cost-effectiveness and production efficiency.
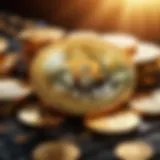
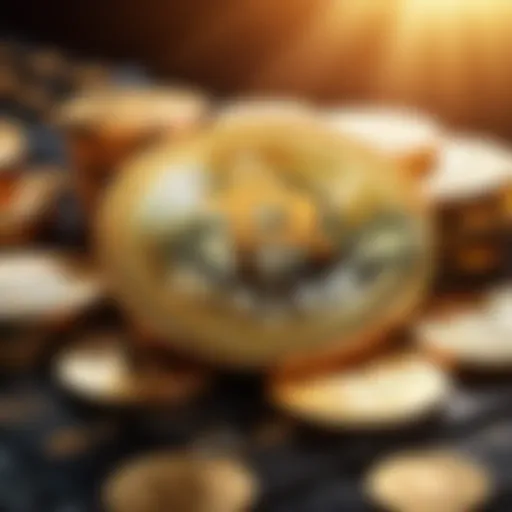
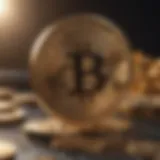
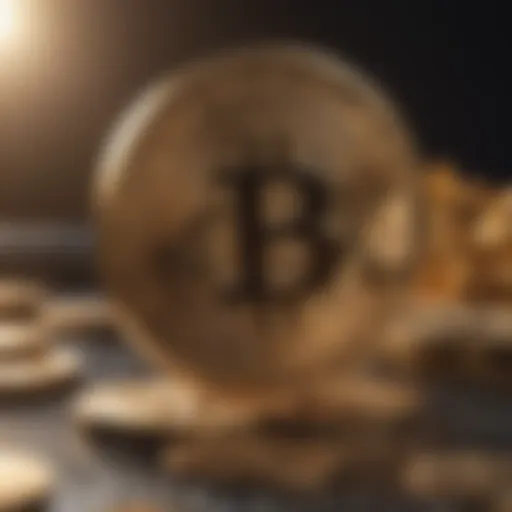